dstroy
Insanely Active Member
I'll update this thread with what I'm working on.
Still in the design process.
Right now I'm working on power stuff.
I'm going to use two power supplies (system voltage 24v), one has a battery backup and will only be used if the power goes out.
Meanwell makes these:
UHP-250-24
PSC-160B
NID-100-12
NID-65-5
Current design:
Main -
UHP-350-24
Backup -
PSC-160B
conversion
-----------------------------
24vdc -> 12vdc (NID 12v)
24vdc -> 5vdc (NID 5v)
24vdc -> 5vdc(NID 5v) -> 3v3 (linear) for sensors
24v -> 10v dimming voltage supply
24v -> 7v mega2560
24v -> 5v -> battery select (3v3) -> m4 express
on battery -- essential
1x NID 5v supply
7v mega2560
5v -> battery select board -> m4 express
on battery -- intermittent
12v NID100 (solenoids)
24v (extraction) -- depends on how big the battery I buy is.
I've got 350w main power, and 160w if it's on battery. Plenty to turn a bunch of shit on and off.
Right now I'm working on the layout for power conversion/distribution
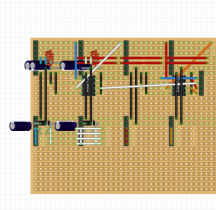
the ICs are panasonic AQW414 (photomos SSR), they are NC and short pin 13 on the Meanwell NID DC/DC converter to ground, which shuts the converter output off.
The caps and inductors are to make them comply with class B emissions
I still have to set up the trim circuits, select the correct barrier diodes so I can OR the 12v | 12v-> and 5v | 5v ->
They just need some schottky diodes.
The two main power supplies needed something different:
Anyway, that's what I'm thinking about. And how to cram all of this in the box I have.
I've got a chunk of heatsink I'm going to use for the UHP350, which I've already lapped flat.
Take it easy
Still in the design process.
Right now I'm working on power stuff.
I'm going to use two power supplies (system voltage 24v), one has a battery backup and will only be used if the power goes out.
Meanwell makes these:
UHP-250-24
PSC-160B
NID-100-12
NID-65-5
Current design:
Main -
UHP-350-24
Backup -
PSC-160B
conversion
-----------------------------
24vdc -> 12vdc (NID 12v)
24vdc -> 5vdc (NID 5v)
24vdc -> 5vdc(NID 5v) -> 3v3 (linear) for sensors
24v -> 10v dimming voltage supply
24v -> 7v mega2560
24v -> 5v -> battery select (3v3) -> m4 express
on battery -- essential
1x NID 5v supply
7v mega2560
5v -> battery select board -> m4 express
on battery -- intermittent
12v NID100 (solenoids)
24v (extraction) -- depends on how big the battery I buy is.
I've got 350w main power, and 160w if it's on battery. Plenty to turn a bunch of shit on and off.
Right now I'm working on the layout for power conversion/distribution
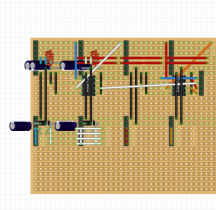
the ICs are panasonic AQW414 (photomos SSR), they are NC and short pin 13 on the Meanwell NID DC/DC converter to ground, which shuts the converter output off.
NID65-MEAN WELL USA Switching Power Supply
MEAN WELL Switching Power Supply. MEAN WELL is a Switching Power Supply manufacturer in Taiwan. – SMPS, SPS manufacturer, AC DC , DC DC , DC AC, industrial power supply, Medical power supply, Din Rail power supply, LED power supply, LED driver, charger, inverter, adaptor, rack power, modular...
www.meanwellusa.com
NID100-MEAN WELL USA Switching Power Supply
MEAN WELL Switching Power Supply. MEAN WELL is a Switching Power Supply manufacturer in Taiwan. – SMPS, SPS manufacturer, AC DC , DC DC , DC AC, industrial power supply, Medical power supply, Din Rail power supply, LED power supply, LED driver, charger, inverter, adaptor, rack power, modular...
www.meanwellusa.com
UHP-350(R)-MEAN WELL USA Switching Power Supply
MEAN WELL Switching Power Supply. MEAN WELL is a Switching Power Supply manufacturer in Taiwan. – SMPS, SPS manufacturer, AC DC , DC DC , DC AC, industrial power supply, Medical power supply, Din Rail power supply, LED power supply, LED driver, charger, inverter, adaptor, rack power, modular...
www.meanwellusa.com
The caps and inductors are to make them comply with class B emissions
I still have to set up the trim circuits, select the correct barrier diodes so I can OR the 12v | 12v-> and 5v | 5v ->
They just need some schottky diodes.
The two main power supplies needed something different:
DR-RDN20-MEAN WELL USA Switching Power Supply
MEAN WELL Switching Power Supply. MEAN WELL is a Switching Power Supply manufacturer in Taiwan. – SMPS, SPS manufacturer, AC DC , DC DC , DC AC, industrial power supply, Medical power supply, Din Rail power supply, LED power supply, LED driver, charger, inverter, adaptor, rack power, modular...
www.meanwellusa.com
Anyway, that's what I'm thinking about. And how to cram all of this in the box I have.
I've got a chunk of heatsink I'm going to use for the UHP350, which I've already lapped flat.
Take it easy
Attachments
-
159.1 KB Views: 112